For nearly 30 years The Phoenix Group has been the Conscience professing that to get consistent part quality and problem free set and run die exchanges, standardization and control of process settings and input variables is the road map to the next successful, problem-free production run.
With the auto industry focusing on mass reduction, some of the first steps were to engineer dies to produce quality parts with substantially thinner mild steels. Last month’s blog touched on selecting and defining material characteristics that will achieve quality panels via computer simulations (virtual die tryout). We learned that reducing the thickness of body panels from .9 mm/1.0mm thickness to the as much as 0.65mm for outer panels was quite challenging to get the simulation correct. These lighter gauge panels were more susceptible to through thickness failure on the press room floor, consistent with formability science.
Light weighting with alternative auto-body materials has also shown that mass reduction of this type has new process requirements; which deviate from traditional draw die design. Aluminum parts utilize less aggressive bead restraints, shallower part designs, larger draw wall angles and larger forming radii. These are a few of the concessions that have yielded successful die production capability, but they have not reduced die maintenance needs. The use of finer grades of abrasives and more frequent die surface polishing it become necessary practices in a successful Preventative Maintenance plan. Beyond more closely spaced Die PM activities, the need for improved die skills and discipline have proven to be necessary to maintain part contact die surfaces, for consistent radius shape, and proper radius to wall tangencies.
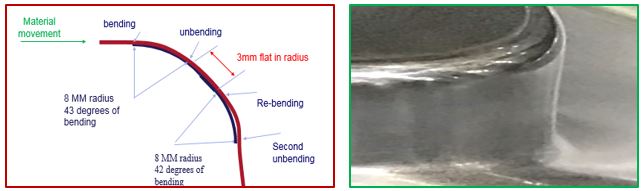
The requirements for reducing vehicle fuel consumption and tailpipe CO2 emissions have resulted in the need to further reduce vehicle mass, while observing the tradeoffs that accompany more stringent crash regulations. Advanced High Strength Steels (AHSS) were conceived, experimentally developed, and eventually mass produced to allow both sets of requirements to be achieved. The use of stronger, thinner materials makes it more challenging to achieve a stable, repeatable process, and thus discipline in stamping process inputs is now even more important. The traditional technique of adding a shim to an equalizer block, or reducing cushion pressure on a specific zone of a programmable press cushion, may eliminate a part split – but the change in the binder gap or reduction in bead restraining force may produce an unacceptable change in localized strains in the part surface. Due to the reduced draw bead size and shape necessary to control an AHSS blank, localized deviations or adjustments in restraining forces can dramatically alter the movement of the entire blank perimeter (an increase of draw-in on the left side of a part can translate to less metal movement on the opposite blank edge). Dissimilar strain conditions (from the original computer simulations) may result in a differential in part spring-back and out-of-tolerance surfaces during a CMM inspection. As the strength of incoming materials have significantly increased, it is often necessary to locally re-cut the die surface to compensate for unpredicted surface distortions. Restraint force changes will nullify the “Morphing” result.
The multiple phases that are present in AHSS materials may result in early flange edge failures not previously experienced in homogeneous mild steel stampings. Adherence to trim and flange steel gap parameter requirements, established through specific edge trim, hole expansion and tensile testing of AHSS (and validated during die construction and tryout) must be adhered to, to produce split free flange edges.
The structural strength output by a cold formed stamping process is a collaboration among the as-delivered material properties, forming geometry and strain hardening capability. dies impact on the parts final thru thickness and shape. Stretching the blank during forming will impact yield strength, dent resistance, and certainly localize thinning, but the final thickness, part geometry and final yield strength result in the final product’s stiffness.
The progress in developing Ultra High Strength Steels that exceed 1 Gigapascal in tensile strength for intrusion prevention and structural rigidity, have resulted in products that cannot be reshaped into a split-free part without the addition of heat energy.
These hot-formed (press-hardened) steels add an additional layer of process complexity to the list of inputs that must be controlled and duplicated on the press room floor. This additional layer or inputs should include but may not be limited to:
- Furnace temperature
- Soak time in the furnace
- Type of furnace (pizza oven rack or rotary storage system)
- Transfer time from furnace to die
- Die closure rate
- Cooling rates, achieved by control of coolant type and inflow/outflow rates (upper and lower die halves, multiple direction thru die)
- Impact of weld areas on heat transfer (local heat transfer variation)
- System heat transfer ability as dies and blanks corrode.
The impact of this additional list of variables may have less importance to the aesthetics of the part surface (lows or wrinkles) but the strength requirements of the part design and the strength produced by the stamping process depend on them. Achieving the desired phase transformation process is completely dependent on and controlled by adherence to the proper process variable settings unique to the Hot Stamping World.